Equipotential Insulators
Equipotential Insulators
A Reliable Solution to a Known Problem
When refining by electrolysis processes, refineries regularly encounter the problem of uneven growth plating on the electrodes, causing short circuits between them. This is a common problem that noticeably reduces the efficiency of the hydrometallurgy purification process, consuming a high amount of energy and time for a limited product yield. The inefficiency of the operation ends up with production at a significantly higher cost.
Unmatched protection for hydrometallurgy
Unlike traditional capping boards on the market, our Equipotential Insulators offer an incredible lifespan, without any maintenance or repair, proven for over 22 years for copper and 19 years for zinc refinery, while also providing unmatched protection against the electrochemical reactions and accelerated corrosion of your expensive equipment.
The very high level of precision of our insulators, from the first to the last electrode, ensures their perfect alignment permanently, resulting in an increase in the quantity and purity of the refined metals and a substantial reduction in short circuits.
Once a short circuit occurs in the electrolysis refining process, the current efficiency decreases rapidly, reducing the yield and affecting the quality of metal plating, in addition to the other stresses mentioned previously.
Why Equipotential Insulators
Our insulators can maintain their chemical stability and technical properties even when exposed to high temperatures. Moreover, these products are designed and manufactured to have remarkable resistance against concentrated thermal stresses. The embedded pultrusion bars are made with a %75 reinforcement volume, which is a proven method for increasing the longitudinal thermal conductivity while decreasing the lateral heat transfer. This results in the rapid dissipation of heat concentration at the contact points when an electrode gets an electrical overload.
It is time to stop using the outdated technology of insulators made of less resistant materials such as plastics that are not able to withstand high acid concentration levels such as 70%. Our chemical formulation for the synthetic resins used in our insulators can easily withstand this level of acid corrosion, and it can hold its performance for over 20 years without any maintenance or repair. This unique formulation resulted from decades of research and development on the selection of compounds in the synthetic resins, with top performance such as resistance to temperatures of up to 600 °C and currents of up to 200,000 Amps at 780 Volts.
Our insulator system protects against all types of damage and corrosion.
Not only our line of insulator products offers a remarkable operation life due to the special chemical formulation, but our design, including high separating walls, protects the electrodes from short circuits by minimizing the possibility of lateral movement. This can also increase the lifespan of electrodes from 2 to 4 times compared to when a traditional insulator is used.
Eliminate short circuits and electrical leakage between adjacent electrodes, and from one cell to another.
When harvesting the refined metal, acid drops fall on the top of the cell, and the chemical interaction between the acid and the concrete at the top of the cell can cause deterioration and reduced durability of the cell, which can eventually lead to structural failure. This can be even more severe when combined with higher concentrations of sulfuric acid as a result of water evaporation due to the heat generated by the refining process, initiating cracks and destruction of vinyl ester or causing deeper penetration of sulfuric acid. Our umbrella-shaped design was introduced to resolve this problem by covering the top portion of the cell walls, and it is used in two types of our insulators, namely Coronary Insulator and Equipotential Insulator with Umbrella-Shape Design.
Coronary Insulator
This type of insulator is designed to act as a secondary insulator between the contact bar and the cell, providing protection for cells against both chemical attacks and high heat concentrations, as well as aligning the standard top insulator in the perfect position.
With their 90-degree edges, these insulators act like an umbrella, preventing acid drops from reaching the cell structure and also redirecting the electrolyte to the cell.
When a major short circuit occurs, different layers of textiles in this type of insulator become a barrier to prevent excessive heat produced by short circuits through the contact bar from transferring to the body of the cell. Hence, it significantly limits thermal stress as one of the known sources of damage to the cells.
Also, cells that already have cracks can benefit from these coronary insulators, and this will significantly extend their remaining lifespan.
Equipotential Insulators with an Umbrella-Shape Design
A coronary insulator can be merged with our equipotential model, resulting in a one-piece insulator system. This type of insulator provides a special slot for positioning the contact bar, and depending on the application, it can provide all the aforementioned advantages in one product.
Demonstration of cell protection with our coronary insulator.
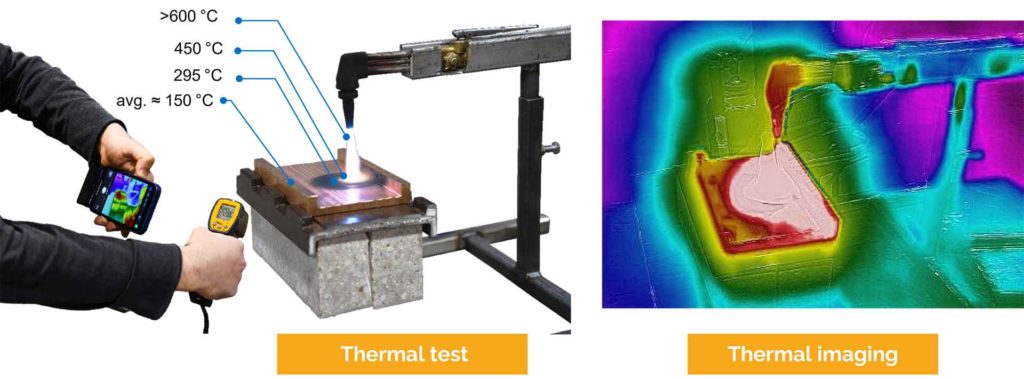
