Hydrometallurgy Electrolytic Cells
Electrolytic Cells
Cells are exposed to unfavorable internal and external factors such as mechanical, thermal, and electrical loads as well as chemical attacks. All of these can have a direct impact on the deterioration and lifespan of cells. Hence, the maintenance and replacement of electrolytic cells can be time-consuming, costly, complex, unsafe, and environmentally harmful.
The protective layer of the cell is the key to corrosion resistance, and our cells are designed to resist thermal variations, thermal shocks, short-circuits, and chemical attacks. Our standard protective layers normally consist of synthetic fiber layers, structural fiberglass, and additional gelcoats due to their high anticorrosive properties.
Composite Cells vs traditional Polymer Concrete Cells
Traditional Electrolytic cells are typically made as a thin-wall polymer concrete container, often with an average amount of fiberglass reinforcement. However, despite the high structural performance of polymer concrete, this type of cell does not offer the best durability and corrosion resistance against acids and thermal stresses. This is more severe by initiation and growth of micro-cracks which makes the concrete walls prone to short-term damages when they come into contact with aggressive acids, such as sulfuric acid.
While there are several conventional methods to reduce the risk of the cell wall from contact with the corrosive electrolyte solutions in electrolytic cells used in industry such as a fiberglass or rubber liner, pre-mature damages will still be inevitable since there is no full bond between the liner and concrete surface. This will subsequently initiate leaks in the cells, resulting in significant losses due to the lack of proper functioning, which is undesirable from both economic and safety points of view. It will affect the operation of the plant and increase risks for operators and maintenance personnel in handling them during operations and maintenance activities at the plant site, and can eventually result in the loss of production and even shut down of the plant due to this issue alone.
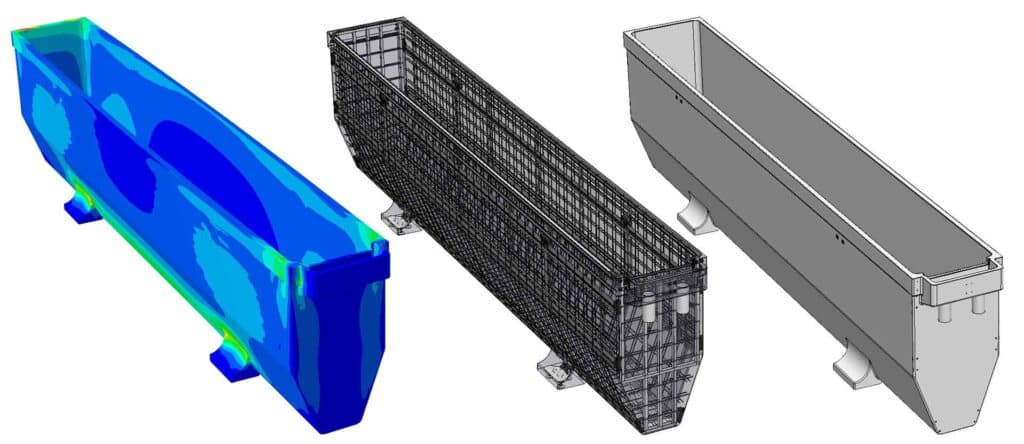
Our composite cells are constructed using a Conjoint Dual-Hull Fiberglass System, in which a highly reinforced polymer concrete serves simply as a core filler between two multi-layer fibreglass laminates. These are all cast and cured at the same time, together with a special gelcoat layer applied to protects these particularly designed laminated skins on the exterior sides, and as a result, the cells are provided with an outstanding operating life.
Challenges in Handling the Cells
There are several challenges related to handling electrolytic cells that are located in close proximity to each other. First, at the time of replacement, the cell has to be unbound from the others. There is also the heavy-duty equipment required, high-amperage electric current in nearby cells, the insufficient space between cells to pass cables, straps, or other lifting equipment, and the limited clearance between the cell and the overhead traveling cranes for safe lifting and maneuvering, especially when combined with the high weight of the cell.
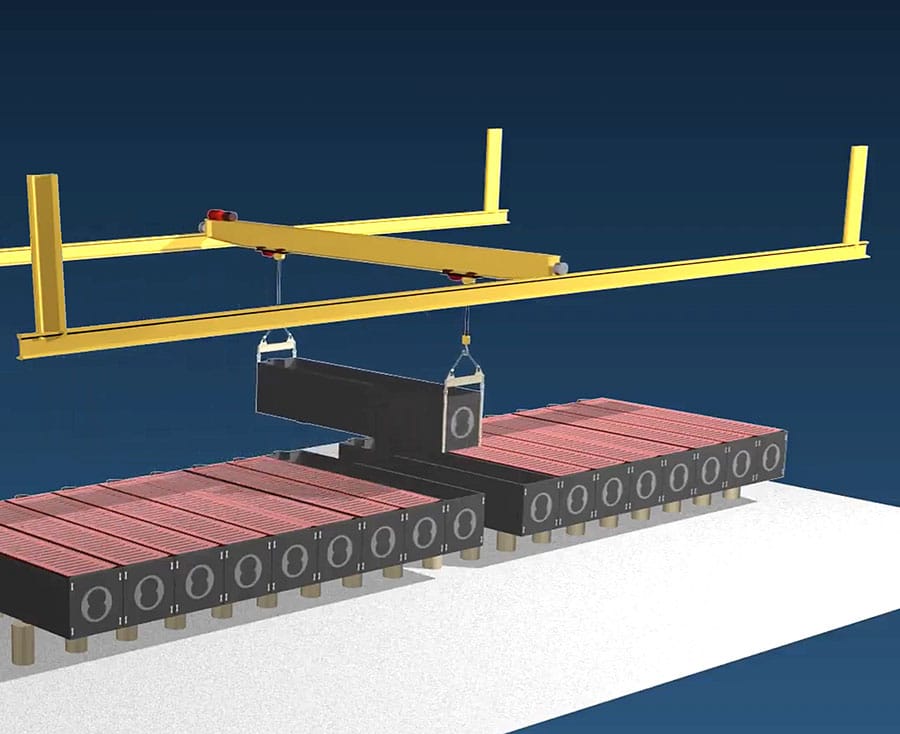
The reported problems have existed since time immemorial, and there has been an increasing need to develop novel solutions to these problems.
Meet our solution to this problem
Integrated Anchor Assemblies
A system that can adapt to fit your needs
While we offer innovative features in our easy-lifting cell technology, for those who don’t have Pultrusion’s cells with embedded reinforcement in the walls, we have developed a new method of anchoring from inside walls to provide a lifting feature that can connect to any lifting equipment.
Inside lifting option: Requires little space between the cell and the overhead traveling cranes for safe lifting and maneuvering.
The combination of the epoxied high-quality fiberglass roving strap and the anchor assembly is a system capable of providing high safety factor throughout lifting.
Quality Control
Construction of cells is conducted according to the detailed description of operations and under a strict quality control program provided by our Department of Production.